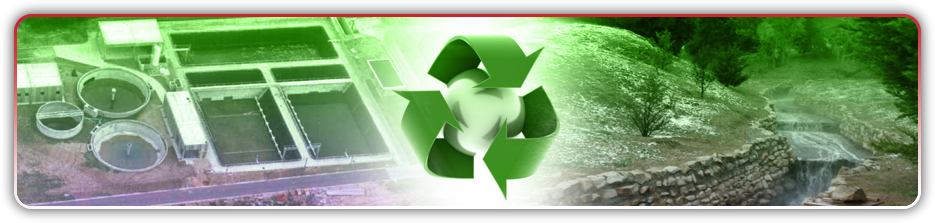
Ecological Commitment
Donto’s environmental responsibility throughout every manufacturing process is evidenced by the acceptance of their products in such environmentally strict markets as the American and the European ones. To such effect, the company uses top brand supplies, which have been tested internationally and approved as environmentally friendly products, at all production stages.
To confirm our commitment to the environment, we have a modern effluent treatment plant with a capacity of 3,600m3 per day, which guarantees the efficient treatment of our effluent and enables us to apply for ISO 14000 certification in the near future.
Description of our effluent treatment plant
Effluent receiving chamberFiltration Basin:
Two-way basin that can filter particles down to 1mm. Effluent is collected into a secondary chamber. Oil and grease are removed by flotation. Waste is placed in containers and shipped to a final disposal site.
Equalization and oxidation basin:
Here, liquids are kept in a homogeneous condition and oxygenated to avoid excessive acidity of the effluent.
Flocculation and Coagulation basin:
Processed and flow controlled effluent is received for flocculation, prior PH correction.
Primary settling tank:
The effluent flows through this concrete settling tank allowing all inorganic material to settle, filtering inorganic sludge out for later dehydration.
Flow splitting chamber:
The effluent flows from the primary settling tank to the flow splitting chamber, which divides the flow into two equal parts and sends it to the biological reactors.
Biological basins:
Ammonia is removed in a pretreatment chamber and then the effluent flows into the biological reactor where bacteria is used for the biological degradation of organic matter.
Secondary settling tank:
After organic degradation, the resulting sludge is allowed to settle and filtered out. The sludge is pumped out and the effluent is discharged into the stabilization pond.
Sludge thickening:
Primary and secondary sludge is stored in a thickener and then removed first by means of screw pumps and then by filtration.
Sludge filtration:
Spin filters used for sludge dewatering. Lime is used to render sludge inert, producing a sludge cake to be disposed in landfills.
Stabilization pond:
1.80m deep pond, located in natural soil, where the water oxygenation process is finished.